How our Batteries are Made
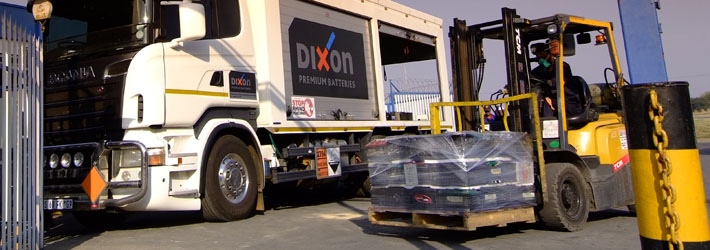
STEP 1
DIXON'S batteries are made with the very best quality for our Customer’s peace of mind. In accordance with our responsibility towards the environment, lead acid batteries that have reached the end of their useful life are efficiently recycled at our manufacturing plant situated in Vereeniging South Africa. The used batteries are broken down and separated into constituent components, namely lead bearing material, polypropylene, polyethylene and spent acid. The spent acid is treated at the effluent treatment plant and disposed of when it complies with the legal requirements.
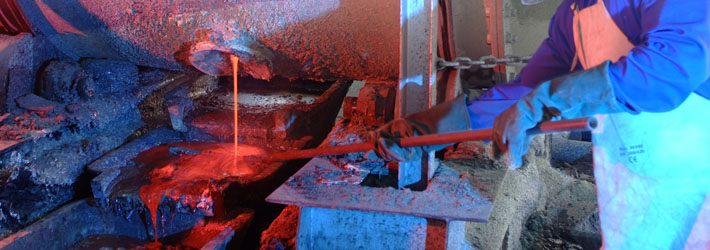
STEP 2
The lead bearing components are recycled at the rotatory reduction furnace. The molten metallic lead is tapped into molds where it is casted into billets. The rotary furnace is fitted with an effective fumes filtering system that keeps air pollution to a minimum and the resulting hazardous furnace slag is disposed of at specifically dedicated dumpsite.
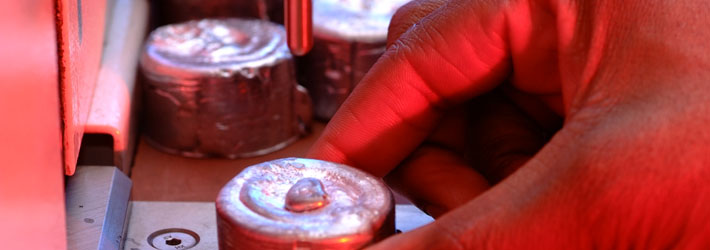
STEP 3
The recovered lead is refined and alloyed at the alloy section. Samples of the molten alloy are sampled at appropriate stages. The samples are carefully casted and prepared for trace element analysis using a spark emission spectroscopy.
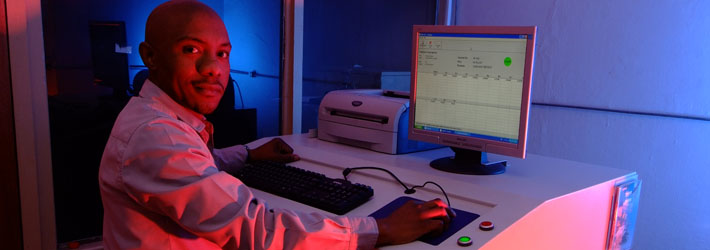
STEP 4
Our competent technical team who analyses the samples also ensures that the spectrometer is effectively and efficiently maintained; calibrated and verified using certified reference materials.

STEP 5
The alloy that complies with strict alloy specification for soft refined lead, lead – antimony and lead- calcium alloys is tapped into ingots for the manufacture of battery grids and lead oxide. The specified alloy composition ensures that the castings have sufficient mechanical integrity to withstand subsequent processing and good battery performance in service.
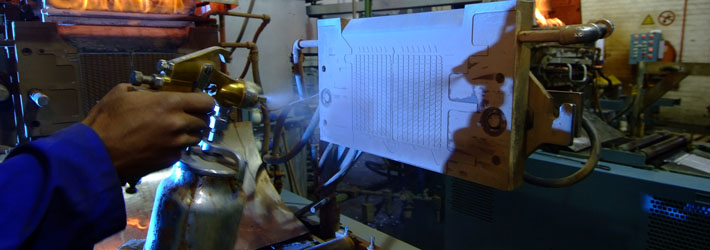
Step 6.0
A skilled operator applies an insulating coat of cork spray. The thickness of the coating layer is such that it allows the molten alloy to flow into the mould impressions and also cool rapidly for economic casting rates. The cork coating optimizes the heat transfer between the molten alloy and the molding surface ensuring that grids of the correct strength and dimensions are produced.
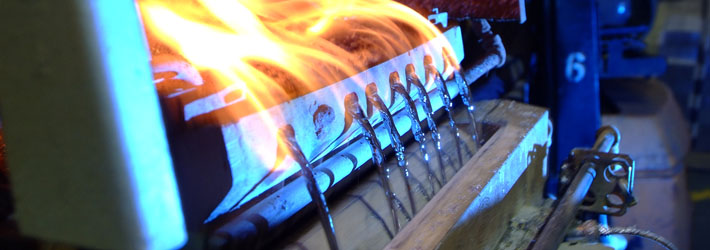
Step 6.1
The grids for the positive electrode are manufactured using the book mould gravity casting process. Molten lead alloy is transferred from the lead pot via a pipe and the ladle dispenser into a split mould. The alloy fills the grid impression which has been machined into the mould block, solidify sufficiently to be ejected, then transferred to a trim die and stacked for age hardening and subsequent pasting process. The temperature and cycle time is monitored and long life grids, free of porosity; shrinkage cracks, dross inclusion and improper grain structure are produced.
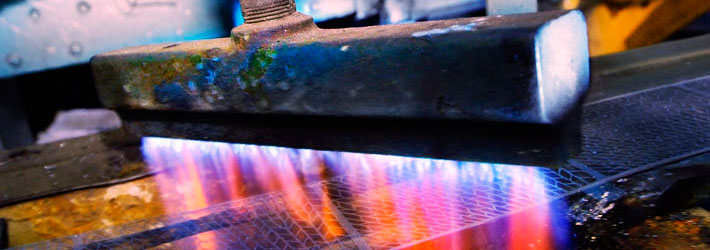
Step 6.2
The continuous casting process, the molten lead alloy is dispensed through the orifices of casting shoe onto a rotating wheel. The melt freezes in grid engravings on the casting wheel to form a continuous grid band. This process produces low weight, high quality in and cost efficiency due to the inherently lower costs of continuous, standardized production of a product, as well as providing increased control over the process through automation.
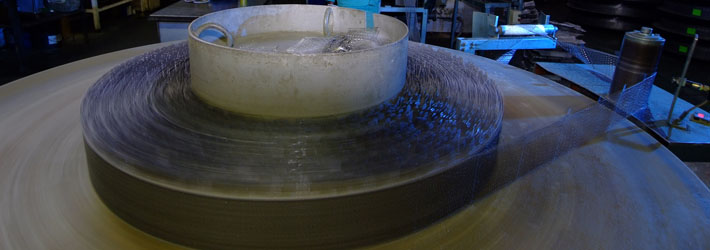
Step 6.3
The manufactured grid band is wound on reels and allowed to age and harden before being transferred to the continuous pasting machine.
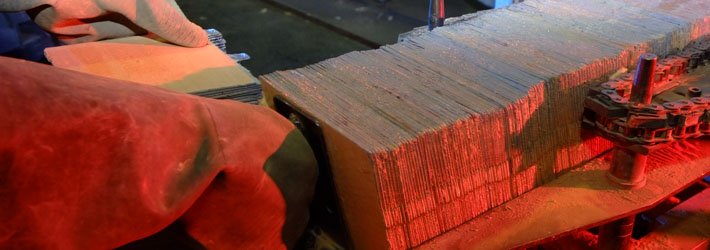
STEP 7
Well cured and dried positive plates are loaded onto the conveyer belt that feed into the fully automated enveloping and stacking machine.
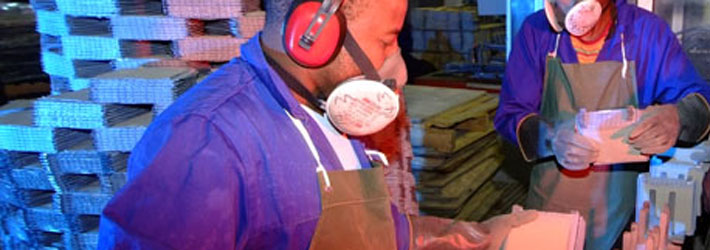
STEP 8
The operator conducts hundred percent inspections of the cells before stacking. This ensures that the positive plates enveloped with the micro porous polyethylene are free of defects before they passed on to the cast-on-strap machine.

STEP 9
The polypropylene material from the battery breaker is melted and force through the circular dies. The hot extrudate, coming out of the die as cylindrical strings are cooled in a water bath.
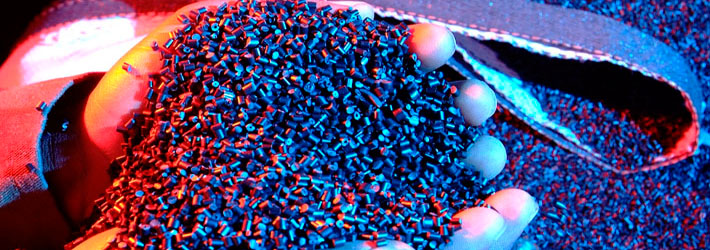
STEP 10
The cooled strings are cut into pellets for use at the injection moulding plant for the manufacture of cases, covers and accessories.
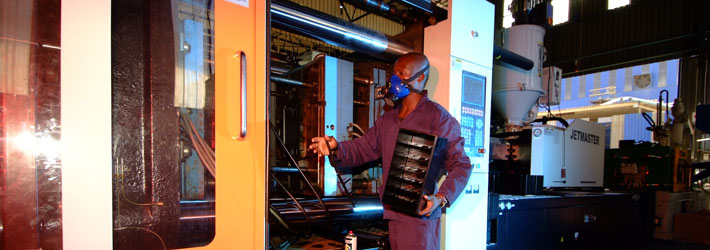
STEP 11
The pelletized polypropylene material is used to manufacture the battery cases, covers and other accessories for the batteries.
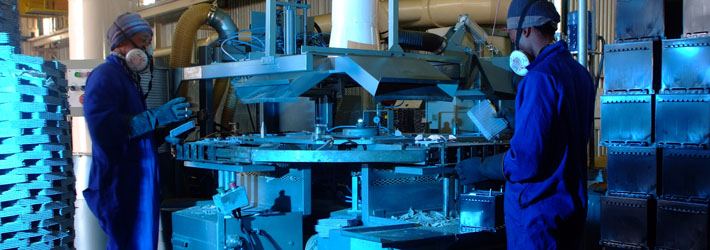
STEP 12
Lead straps are formed in a mould to weld all the positive and negative battery plates together to form a cell. Individual cells are then passed through a short circuit tester to check if any electrical shorts exist between the positive and negative plates.
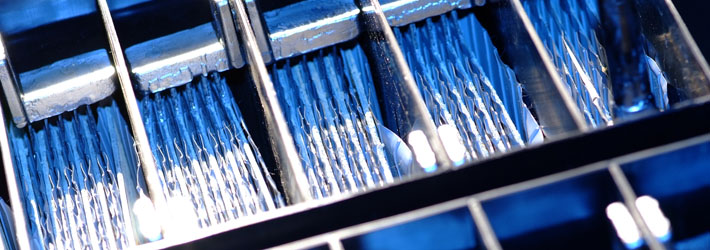
STEP 13
To achieve a battery voltage of 12V, six cells must be connected in series. Connections from cell to cell for automotive batteries are made within the polypropylene container through holes punched in the partitions. The positive - strap terminal on one side and the negative strap terminal on the other side of the hole are pressed together and welded.
This delicate process of intercell weld is done by highly automated line to ensure consistency and reliability. The integrity of the weld is routinely shear tested, since if any one of the six intercell welds per battery does not fulfil the specifications, the battery will be scrapped.
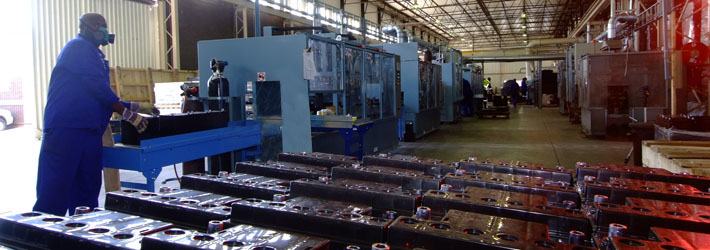
STEP 14
Weld batteries are passed through a fully automated heat sealing line were the battery lid is sealed onto the battery case. The batteries are pressure tested with automatic leak testing machine and those which do not comply with the specified testing pressure are automatically ejected from the production line.
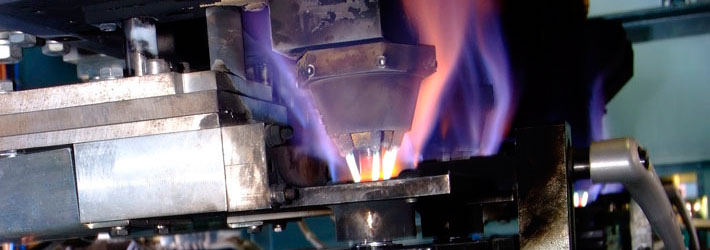
STEP 15
Our post burning machine is designed to do the final joining operation on the attachment of car battery posts. It has an auto memory unit capable of storing multiple processes for ease of model changes and precision tooling to make high quality posts. The machine has very precise flame control function with a proportional – integral-derivative controller (PID controller) which is critical for this application.
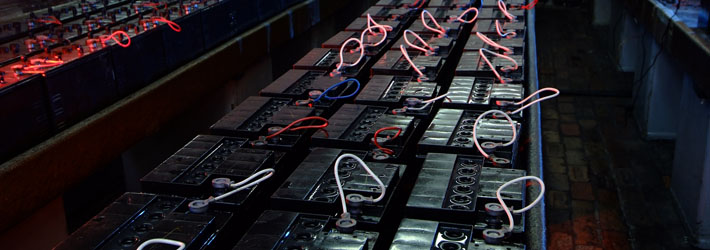
STEP 16
The formation is conducted in two stages, a process called two-short formation. This is done to optimize the formation of β-PbO2 which is the major contributor to improved battery performance.
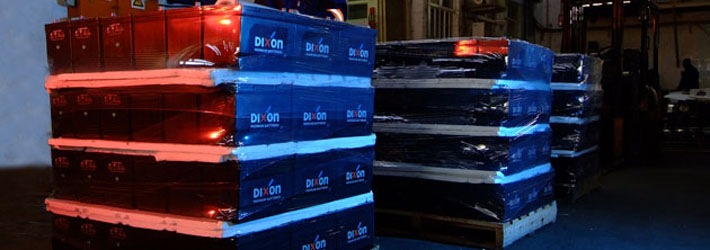
STEP 18
Our efficient packing team then uses state-of-the-art equipment to carefully package each and every battery. This ensures DIXON Premium Batteries arrive at their destination in the same pristine condition as they have left the factory.
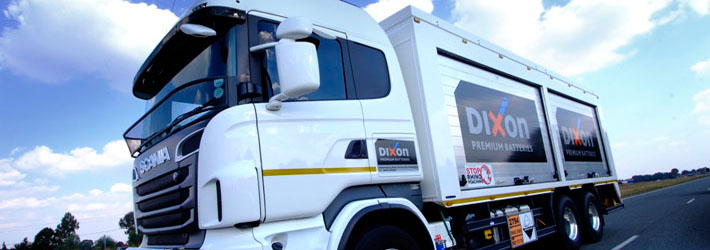
STEP 19
DIXON Batteries are transported in a proudly branded fleet of “DIXON” trucks that deliver our batteries throughout South Africa, Botswana, Swaziland, Lesotho and Namibia.